The Dynafill Beer Filler – Fills and Crowns in a Single Unit
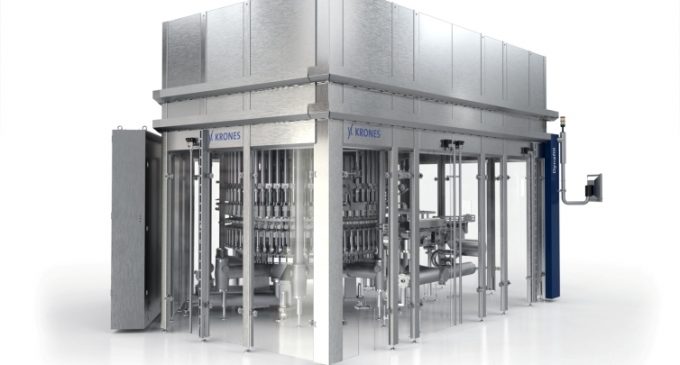
Beverage bottlers’ requirements are extremely exacting: achieving progressively higher outputs while consuming less CO2 and nonetheless upgrading the filling quality – and all this in a sturdy system that’s ideally designed for cleaning. For beer filling, these are precisely the criteria Krones has satisfied with the new Dynafill.
And this product has some persuasive pluses that compel respect: the machine halves the time required, saves distance, and replaces what used to be two machine units with a single one. How is this accomplished? The Dynafill performs filling and crowning in a single functional unit – and needs only five seconds for it. It can safely be claimed that the Dynafill concept is revolutionising beer bottling.
The filling process in detail:
- Evacuation and filling
The filling valve moves into the pressure chamber; the glass bottle is pressed against it. The container is flushed with CO2. The filling process itself then takes only around half a second, and ends when the bowl pressure has been reached inside the bottle.
- Crowning and snifting
The closure is inserted and the chamber sealed while the flushing operation is still ongoing. In parallel to the filling operation, the pressure chamber is then evacuated, and pressurised with CO2. Once the filling valve has completed its task, it moves back and makes way for the crowner head, which places a crown on the bottle. The bottle descends, and leaves the filling and crowning unit.
All Advantages at a Glance
- Reduced footprint – Thanks to the 2-in-1 principle, the Dynafill needs significantly less space than a comparable filler-crowner combination. Moreover, since the filler does not have to be emptied in the event of a malfunction in the bottling line, the buffering section to the labeller can be downsized and the labeller can be directly block-synchronised with the filler.
- Higher outputs – The Dynafill will enable higher overall line outputs to be achieved than with conventional systems.
- Enhanced filling quality – The enclosed hygienic filling and crowning zone ensures optimal product purity, since no return gas has to be sent back to the product bowl. Moreover, no fobber is required, and no product is lost during filling.
- Reduced CO2 consumption – The CO2 consumption is 20 per cent lower than with conventional systems.
- Stability in the filling process – The Dynafill can handle beverages in both coldfill and warmfill (temperature up to 30 °C) modes – the process duration is less than five seconds and always remains stable.
- Ideal interior cleaning – The Dynafill is a closed system. The filling valve and the crowning unit are integrated into the CIP circuit.
- Easier accessibility – The individual components involved, like the filling valve, the media piping and the drive of the crowning head can be individually removed.