Springhill Farms Upgrade – Biomethane to the Grid and CO2 to the Tomatoes
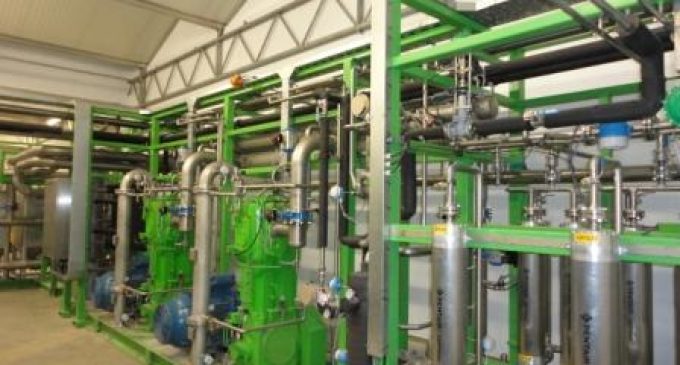
In the heart of the English countryside, Springhill Farms makes the very most of agricultural waste. Upgraded biogas is injected into the national gas grid, while the carbon dioxide (CO2) by-product goes straight to the farms’ tomato greenhouses.
The gas produced during anaerobic digestion consists roughly of 60 percent methane and 40 percent CO2. Until recently, biogas from anaerobic digestion was only used for local heating or power generation, but a much more economic yield is gained by upgrading biogas to biomethane (biogas with the specifications of natural gas).
Upgrading technology turns raw biogas into biomethane by removing impurities and CO2. The next step to commercial viability is bringing this gas to the grid. While this business model is becoming more attractive, it is not straightforward. The best investment decision depends on the volume and characteristics of the feedstock, the national legislation, and the right technology.
Membranes & Cryogenics
As the expertise and technology matures, the days of pioneering enthusiasts and farmyard experiments are over. By opting for Pentair Haffmans’ combination of membrane and cryogenic technology, Springhill Farms has leapt beyond the tight margins of traditional biomethane production.
The Vale of Evesham in Worcestershire, situated in the River Avon basin, is known as Great Britain’s ‘fruit and vegetable basket’. One of the region’s main producers, Evesham Vale Growers, needed to find a solution to a mounting waste problem and the rising costs of power and heating. Due to new legislation, the waste from 2,000 acres of farmland and 30 acres of glasshouses at Springhill Farms could no longer be returned to the land as fertilizer. The construction of an anaerobic digester plant combined with biogas upgrading and grid injection as well as CO2 recovery, has created a win-win situation.
Higher Methane Yield & Pure CO2
“It has been a long way to achieve the best solution, but in the end we have succeeded in creating a farm that produces food and energy on an economically and environmentally sustainable basis and can serve as an example of the farming of the future,“ says Matt Powell, Director of Springhill Farms.
Pentair Haffmans’ solution to separate the biogas stream allowed Springhill Farms to produce more than biomethane. “With conventional techniques the CO2 by-product and a considerable amount of methane is expelled into the air and is simply lost,” says Niels den Heijer, Pentair Haffmans’ product manager for CO2 & Biogas Systems. “This means not only economic loss but also environmental damage. As a greenhouse gas, methane is about 22 times more harmful than CO2. Our system includes a unique second process step, during which the off-gas is cleaned and the environmentally harmful methane slip is completely eliminated.”
Pentair Haffmans’ two-step approach results in a higher methane yield and allows for recovery of pure CO2. At Springhill Farms, the liquid CO2 is produced during the night and used in the daytime as a gaseous natural fertilizer in the farms’ greenhouses. The system configuration enables precise CO2 dosing based on a set timetable that assures optimal plant growth and a 15 percent higher tomato output.
While Springhill Farms uses the produced CO2 for internal purposes, other plant operators sell the liquid CO2 and generate an additional source of income.
Since August 2013, Springhill Farms has delivered biomethane to the Wales and West Utilities gas grid. At full capacity, the system produces 225 Nm3/h of biomethane 24/7, which is enough to supply 1,000 households with their annual natural gas consumption. Springhill Farms uses 25 percent of the gas produced to meet its own heating and power needs.
Having met its original goal of energy self-sufficiency and waste processing, the farm has diversified, and Vale Green Energy has new plans for sustainable local energy production.
“We are already occupied with the next step, a new farm and digester that is four times as big as our current operation, and will be operational in Q3 2014,” Powell says. “We believe in the concept and have again awarded the biogas upgrading part of this project to Pentair Haffmans.”
For further information visit www.foodandbeverage.pentair.com.
KEY FACTS
Product – Advanced Plus system Technology Membrane/Cryogenic
PLANT CAPACITY – Biogas 500 Nm3/h Biomethane 225 Nm3/h CO2 3,000 tons per year
Methane Usage – Injection into gas grid according to UK specifications
CO2 Usage – yes
Biogas Source – Vegetable-based material
Benefits – Full process control without methane slip – CO2 as a profitable product – Low Total Cost of Ownership.