Loma Service Hits Over 90% First Time Fix Rate
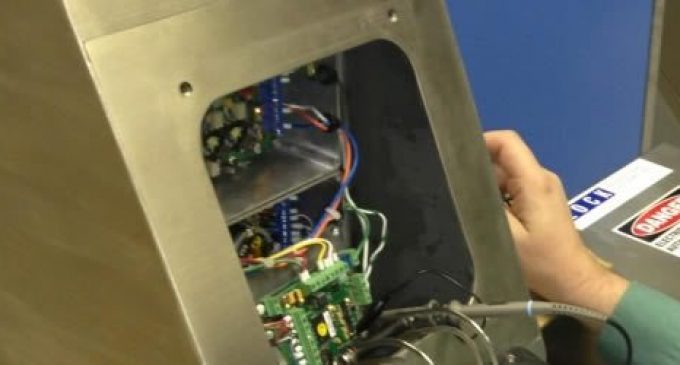
Further underlining its position at the forefront of inspection equipment for the global food industry, Loma Systems’ service delivery continues to lead the market. The company is attributing its unrivalled 91% first time fix rate to the powerful remote diagnostics tools now available with its range of high performance metal detectors, checkweighers and X-ray units, backed by a dedicated service team, guaranteed next-day response and bespoke preventative maintenance agreements.
At a time of year when maintaining uptime is more critical than ever, food packers and processors running automated integrated production lines are aware that any single in-line component failing can stop all production. A lack of regular maintenance will inevitably lead to an increased risk of downtime as components wear out. As a result, access to a reputable after sales and service team is essential.
In line with its ‘Designed to Survive’ ethos and commitment to delivering maximum uptime at a low lifetime cost of ownership, Loma’s aim is to ensure the long term reliability of its equipment. With outstanding after sales support a key component of this, the company measures two key elements of its service delivery, Response Time and First Time Fix Rate. On average, across all service call outs in the UK, Loma is achieving more than nine out of ten problems fixed, within one working day from the time the problem is first reported.
A vital part of Loma’s market-leading service delivery is the powerful remote diagnostics tool offered with its robust and reliable in-line inspection systems. This gives the company full real-time visibility of installed equipment and can be used to make a speedy diagnosis, allowing the company’s technical specialists to quickly understand the problem.
Loma’s remote diagnostics significantly reduces downtime, often allowing faults to be fixed in minutes. It helps prevent system failures, provides fast resolution of diagnosed problems and increases overall reliability, operation and performance of an inspection system.
If the fault or breakdown is more serious and cannot be fixed remotely then one of Loma’s field technicians will conduct an on-site visit. With remote diagnostics, Loma can ensure the technician arrives quickly, with the right parts, and has the necessary training to perform a quick and effective repair.
Loma’s dedicated service teams benefit from first class in-house training, as well as an in-depth understanding of customer’s products and food industry applications.
Tony Bryant, UK Sales Manager at Loma Systems says: “The integrated remote diagnostics tool has helped revolutionise how we deal with our customers and enabled us to offer a truly unrivalled level of service. It means that by investing in Loma inspection systems, food packers and processors can virtually eliminate unplanned downtime and boost their bottom line. Plus by planning ahead and utilising one of our three bespoke preventative maintenance agreements, customers have the peace of mind that whatever the issue, they will be taken care of with competent and expedient support.
“Our service department’s sole focus is to support customers’ equipment and keep production lines running,” he concludes.
Loma offers a three-tier bespoke preventative maintenance package comprising 5-Star, 3-Star and 1-Star service agreements. Each contract is tailored to the business and equipment needs which provide a number of benefits including maximum machine performance, guaranteed advanced bookings, control over expenditure and elimination of problems before they arise.
For further information contact Loma Systems on Tel +44 (0)1252 893300 or visit www.loma.com.