Lete SpA – A Compact Line of 44,000 bph For Square Bottles
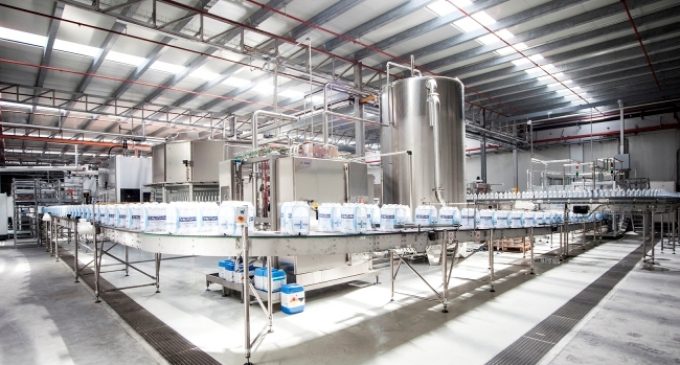
Lete is an internationally recognised trademark, thanks to the peculiarity of the naturally sparkling water and also because it is the main sponsor of Napoli Calcio. The collaboration with ACMI dates back more than twenty years and the famous Italian supplier of end-of-lines has always considered Lete SpA to be one of its most prestigious customers.
The line in question is a PET line of 44,000 square bottles per hour and was designed according to the “compact line” concept, that is, eliminating any accumulation tables except for the one at the blowing-filling block outfeed, the only element, along with the labeller, not supplied by ACMI. The labeller-shrink wrapper connection is managed by special software thanks to which ACMI is able to coordinate the production oscillations of the two machines so as to create a continuous flow of products. This also makes it possible to efficiently handle unstable products and products with very thin walls, just as in the case of the two litre bottle designed for Lete. It is important to point out that the software developed by ACMI interfaces with the major labellers on the market.
Thanks to the use of a specific gate system the 2 litre square bottles reach the double infeed Fenix 275 model shrink wrapper infeed perfectly aligned. The machine, which reaches a maximum speed of 150 packs per minute, is equipped with the automatic film changeover system, a system which makes it possible to switch from the film of the finished reel to that of the new one in a time of about ten seconds without any intervention by the operator. The two reels with the shrink wrap film are housed in a functional and ergonomic external box in which the operator can work in complete safety away from any moving part of the shrink wrapper.
At the shrink wrapper outfeed the packs perform a wide run to meet the specific requirements of the plant layout and reach the double infeed Viper 2P model handle applicator. The Viper handle applicator range is characterised by the electromechanical spacing system that avoids the use of the traditional spacing screws. This has a number of advantages including the reduction of occupied space, the absence of rubbing on the packs and the high simplicity in the format changeover operations.
At the handle applicator outfeed, the packs reach one of the main innovations introduced by ACMI, the high speed Compakt HS model palletiser with “low level” infeed. This innovative palletiser, which reaches a maximum speed of 520 layers per hour with interlayer application, is fed by the 3 module Twisterbox layer formation system. The 3 module configuration is the fastest possible and it is the only one that allows you to keep up with this new type of palletiser.
The Compakt HS structure consists of a series of mobile platforms and an automatic interlayer insertion system which allows synchronised movement of the various palletisation phases reducing to zero both the pallet changeover times and the interlayer insertion times.
Furthermore, another important aspect which should be pointed out is that the handling of the product takes place by means of motorised belts in all its phases and never by means of bars or mechanical pushers. This allows you to obtain a series of advantages among which it is interesting to highlight the high operating speed and the possibility of treating unstable and fragile products.
At the palletiser outfeed, ACMI installed two Vortex 1000 model stretch wrappers with an automatic reel changeover and electronic pre-stretching system. The main reason for the choice of installing two stretch wrappers in series can be attributed to the possibility given to the customer of also producing half pallets, for which one single stretch wrapper, as fast as it might be, would not be enough.
Built with a robust steel structure, Vortex is a “fixed pallet” and rotating ring stretch wrapper. The most interesting characteristic is its electronic pre-stretching system that makes it possible to pre-stretch the film to a maximum value of even more than 400%. It is also possible to fully customise the wrapping cycle so as to achieve the best wrapping possible in any condition and with any product.
The Vortex stretch wrapper can reach a maximum speed of 150 pallets per hour and, in the installation in question, it has been equipped with the top cover dispenser system. To conclude, we can actually say that the PET line installed at the Lete plant is the maximum technological evolution available today on the market.