Lean – New Horizons and New Challenges
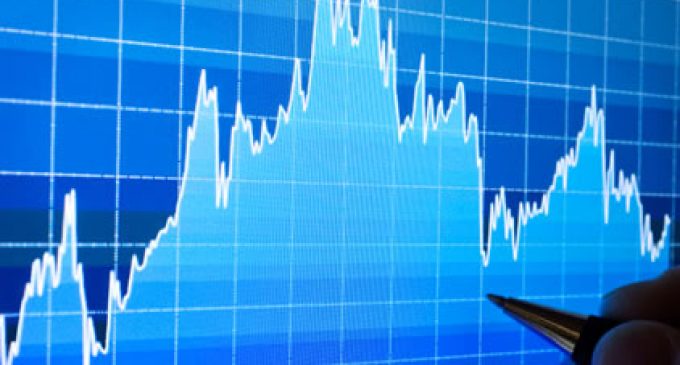
Good industry practice over the past 30 years has shown that major efficiency gains can be achieved through the application of a Lean Manufacturing strategy. However, global economic pressures show few signs of abating and manufacturing companies who may already be implementing Lean are responding by looking for ever new ways of managing ongoing cost pressures and operating constraints.
Gill Bowen, MPL Group Managing Director, observes that, amongst MPL clients, margins are being squeezed in the FMCG space with shorter product refresh cycles, lower volumes and margin pressure. Consequently brand owners are seeking to streamline their operations to focus only on those aspects of their manufacturing process which generate core value. Other activities can be outsourced. This is giving rise to a new era of mobile, often agency-based labour, co-manufacturing and co-packing partnerships and outsourced logistics.
This brings an excellent new opportunity to drive cost out of the manufacturing and delivery chain and improving flexibility improves competitive position. Lean provides a strong methodology to make the entire process efficient, but this new world brings further challenges. How to control, implement and sustain process management across multiple links that cross different geographic locations and even different companies? Service level agreements between different links in the process chain need to be created and managed. How to make this chain fluid and flexible while still maintaining tight control?
One of MPL’s clients, an international confectionery manufacturer, uses large pools of temporary labour to meet varying demand and to remain agile in a diverse group of operations under one corporate umbrella. Their challenge is to manage this pool of labour to ensure the right level of skill is available at the right time in the right place, whilst trying to manage the agency costs to whom the labour supply is contracted This involves a connectivity of international management and local operations planning coupled with traditional lean techniques to gain the greatest efficiency of labour. Implementing a labour planning system that couples the production to the agency supply has already resulted in cost savings of over a million pounds in just a few months.
Another MPL client is a major manufacturer of snack products who wish to focus their operation on their core competitive advantage of a special form of baking. On that basis they are in the process of outsourcing to co-packing and co-manufacturing organizations many of the end product packaging, logistics and product trace functions. This entails the need to implement end-to-end service level agreements and KPIs across multiple sites and several companies. MPL is working with both the insource and outsource elements of this chain to extend well proven Lean techniques across the boundaries supported by the power of its web based Advanced Lean Driver software platform. KPI measures developed from the short interval control process will become critical commercial factors in measuring the performance of this chain.
Alan Edwards, an MPL Director, has been working with a major fresh food manufacturer to create a management level set of common KPIs across a diverse business where plant consolidation and business margin improvement are core strategies. Traditionally each plant has run an efficient operation targeting OEE as the core measure of performance. The challenge is that this KPI is constructed slightly differently for each operation and this makes comparison challenging. By using a common measurement methodology and linking the KPIs through a common web connected platform, this enables management to become more agile and to start to connect operational KPIs with the more general business led measures of profitability. With an increasing presence of Private Equity ownership in the industry where investment teams are more focused on financial results than long term allegiance to a specific project, then developing this common language is becoming essential for communication.
Beyond Lean itself and the technology used to capture and move information between operational elements, there also becomes a strong people behavioral challenge. Dr Peter Bowen, MPL founder and a three-decade veteran of deploying Lean techniques, points out that establishing a common purpose across these diverse elements of the manufacturing chain is a key challenge. Improving the Lean coaching cycle and implementing easy to use mobile tools will become critical elements to making this aspect work.
Over the past 28 years MPL, through its 400 plus client projects, has witnessed the evolution of Lean into a stable and reliable strategic tool to reduce cost and drive efficiency. Ex Microsoft veteran Graham Brant has recently joined the MPL team to lead the development and deployment of Lean-based web platforms. Graham is working with clients to embrace latest anytime/anywhere information technologies using cloud based web enabled tools. These are now extending the proven power of Lean methodology across organizations and between different companies. Working with its clients, MPL is delivering a new style of manufacturing operating system. This platform is able to deliver the flexibility and most importantly the sustainability that is necessary to support business in today’s fast evolving FMCG environment.