Laser Sorting Technology Enhances Pea Quality at Birds Eye
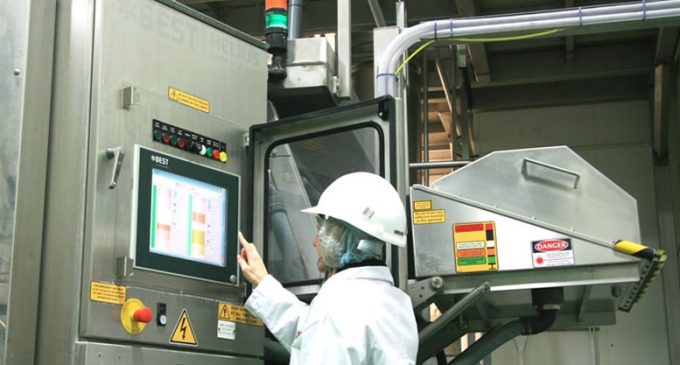
TOMRA Sorting, exclusively represented in the UK by Stein Solutions, has supplied two Best Helius™ free-fall laser sorters to Birds Eye’s Lowestoft f actory in order to provide greatly enhanced quality checks for the company’s market-leading frozen peas.
Birds Eye, part of Iglo Foods Group, says that the new sorters are allowing a far greater number of contaminants to be detected and removed – up to 99.5% efficiency for most defects – while reducing the overall yield loss of each production run by as much as 50%. In addition, overall throughput has risen by 33%. As a result, the sorters are delivering a return on investment of less than one year.
The Birds Eye factory processes and packs 36,000 tonnes of peas each year. The peas are frozen within two and a half hours of being picked and then called into the factory as required for cleaning, grading and packing. Typical contaminants that need to be removed include caterpillars, snails and stones from the soil, and pods and other parts of the pea plant.
Detecting Defects and Contaminants
The Helius™ uses laser technology to detect all types of colour and structure defects in a stream of good product. In addition, thanks to its patented FLUO™ technology, the machine is also able to spot contaminants by assessing biological characteristics that are invisible to the human eye. For the sorting of peas, it can detect the slightest shades of chlorophyll to distinguish between good products and defects. This makes it far more sensitive and accurate than the camera-based systems using UV light that it has replaced.
“Caterpillars were a major weakness with our old system,” explains Quality Assurance Manager Paul George, “since if they were rolled up into a ball they were not easy to distinguish from the shape of pea. Similarly small parts of the pod could be missed as they were very close in colour to the pea.
“The Helius™ sorters, by comparison, have an efficiency rate of 99.5% for caterpillars and minerals, and 98% for pods. This level of accuracy means we can harvest more of the crop initially. Equally important, the reject system is more accurate so that we lose fewer good items during the process. This has allowed us to increase the quality of the product while also increasing the overall yield.”
The two Helius™ machines have replaced four of the older models from a competitor and this has freed up staff to carry out other duties on the line.
More Reliable and Accurate
“Our old equipment needed regular monitoring but the Helius™ sorters are far more reliable,” confirms Paul George. “We also find the freefall sorting system works better than a belt in achieving more accurate rejection rates.”
In addition, the Helius™ laser technology provides a more consistent operation compared to fluorescent tubes which can deteriorate over time. Equally important, the machines can continue to function in both extreme hot and cold environments.
Birds Eye says that the installation of the equipment went smoothly. Full training was provided for operators at TOMRA Sorting Food’s headquarters in Belgium.
“We have an excellent working relationship with Stein Solutions and TOMRA and this ensured that the installation process was seamless and well-managed,” comments Jon Wetherell, Birds Eye’s Project Engineer.
The factory processes and packs 12 tonnes of peas per hour into a range of pack sizes from 400g to 1.37kg, as well as smaller 286g bags of Petit Pois, working 24 hour shifts, five days a week.
“Thanks to the efficiency of the Helius™ sorters cleaning is no longer an issue in terms of packing speeds,” says Manufacturing Manager Ashley Skelly. “Indeed, we could run the machines faster but final throughput is now governed by the speed of some of the equipment downstream of the sorters.”