KHS and Schubert Supply Swiss Brewery With First Jointly-developed System
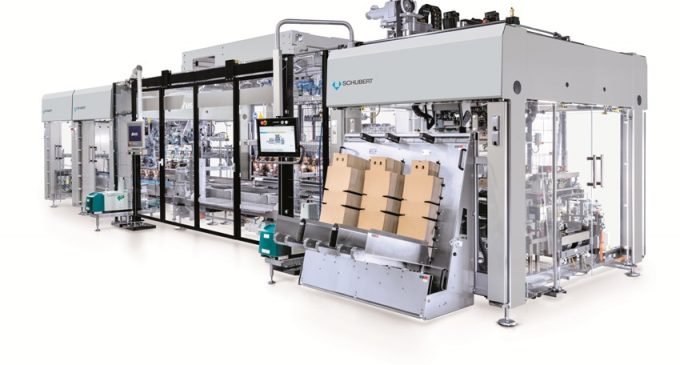
KHS and Schubert have combined their expertise to offer beverage producers a complete and powerful package to fill and pack their products in the future. A first example of the successful partnership is the block solution for the Schützengarten brewery, already implemented in the Swiss canton of St. Gallen, which can process many different bottle and final-package formats – while taking up very little space.
The traditional Schützengarten brewery is not only popular in Switzerland for its creative speciality beers. With a large number of package designs that come in different shapes and sizes, and its bespoke and embossed bottle designs and shapes, the company really stands out from the crowd. Founded in 1779, Schützengarten might be Switzerland’s oldest brewery, but it uses the latest technology to manufacture highly distinctive products of exceptional quality on an international scale. This vision includes a wide range of specialist beers: Some beers contain exotic ingredients. For example, Brown Ale gets its distinct aroma from juniper berries. Radler contains Edelweiss extract which adds a subtle bitter note, complementing the fresh citrus flavour of this mixed beer beverage. And for their Chocolate Sweet Stout, the Swiss even source their Cocoa from Trinidad. But the lion’s share of sales is generated by the traditional Schützengarten Light Lager. Schützengarten has been independent since its foundation, and currently has around 220 employees. The 175,000 hectolitres of beer produced every year in its various guises are largely supplied to the hospitality and catering industries. The company supplies a further 130,000 hectolitres of commercial products ranging from water, through to quality wines and Champagnes.
Growing customer expectations
The final packaging is just as varied as the product range. As well as four-, six- and eight-packs, the Swiss market also demands ten-packs and even 18-packs. During special campaigns involving supermarket discount chains, cartons of 12 and 15 are also produced. Of course, classic beer crates are still part of the range. “The development of packaging variants has been explosive in recent years – we just cannot ignore what the market wants,” says Dr. Martin Ketterer, Technical Director and Member of the Schützengarten Management Board.
The downstream dry section of the filling unit is particularly important for the successful management of such complex packaging tasks. This is where bottles are grouped in different arrays and packaged, and where any special offers are given their own individual face. This is why the company invested in a new line with a state-of-the-art dry section: It is a multifunctional system developed by
KHS and Schubert which hasn’t previously been available on the market in this form; it consists of a KHS packager and a Schubert TLM unit.
The Swiss brewery’s order included an unpacking / packing unit, a binder / unscrambler and a combined palletizer / depalletizer, complete with a new glass depalletizer. A pallet wrapper, a crate washing system and an automated plastic crate buffer storage magazine are also part of the complete installation. The new system achieves an output of 25,000 to 35,000 bottles per hour. In addition to six different plastic crates for the reusable bottles, Schützengarten packs various carton formats with quantities of six to eighteen bottles on the new system.
Modular block design
In the past, KHS has offered classic production lines for processing baskets and/or cluster packs, whereby individual machines were linked by transportation systems. The new block solution called Innopack TLM combines the individual modules so that additional transport units are dispensed with, and a compact unit obtained. “With KHS’s many years of experience in designing bottling plants and the specialist skills of the Schubert Group in the final packaging of a variety of products, we are now in a position to offer the beverage industry a solution combining proven standard components from the two companies,” claims Kanellos Tzinieris, the beverage industry specialist in Schubert’s sales team.
With its modular design, the Innopack TLM offers a high degree of flexibility; essential for managing the variety of products. “We offer space-saving solutions that are flexible and can be expanded, in case production increases, or if the formats and product composition change. Customers can therefore respond quickly to changing requirements without immediately having to invest in a new line,” says Peter Gabriel, Managing Director of Schubert GmbH Verpackungsmaschinen, who is responsible for strategic planning of the joint venture. Currently, eleven different bottle formats are being packaged on the block system, including seven reusable and four disposable bottles.
A fast connection on rails
In this case, the Transmodul robot is the mechanical transport link between the KHS packer and the Schubert modules. The Transmodul uses a connector to move into the KHS packaging machine. Thanks to the inductive power supply and wireless transmission of data and signals, the Transmodul can move freely. “Without the Transmodul, merging our plants would not be feasible,” explains Kanellos Tzinieris. In the first TLM module, the cartons are erected, glued and set down on the Transmodul which moves them into the KHS packaging module. Here, the bottles are automatically inserted into the cartons in the right quantity and configuration. Subsequently the filled cartons are passed by the Transmodul to the TLM sealing modules, where F2 robots seal them.
“The block formation from KHS and Schubert components makes long transfer systems and separate infeed and outfeed sections redundant,” Lutz Müller, KHS Sales Manager for Switzerland, explains the compact machine design. He adds: “This reduces maintenance, wear and tear, and energy consumption. Furthermore, this compact installation requires only one operator.” Operation is also made easier by the interchangeable formatting tools which always enable operation with the same basic settings. This reduces changeover times to less than 15 minutes.
Thanks to this block packaging solution, Schützengarten can now use the filling capacity to its fullest extent, even in a tight space. This results in an almost doubled line capacity compared with the previously used packaging solution. The packaging line can now package crates, and soon it will also be able to handle baskets, clusters and other carton-packed variants. “The block packaging system opens up a whole host of new possibilities for us. We are now ideally set up for the future, and we have solid partners on board,” says Dr. Martin Ketterer. The joint project with the Swiss Schützengarten brewery has been successfully launched. In the meantime, a further three orders have been received. Others are sure to follow, because the concept as a whole helps bottlers look to the future and promises great opportunities for beverage producers.
The collaboration between KHS and Schubert
The jointly developed block solution from KHS and Schubert stands for maximum flexibility and compact design. In conventional production lines for packing beverage bottles in baskets or cluster packs, individual machines are connected by transportation systems. Innopack TLM connects the Schubert and KHS machines inline by assembling the individual modules into one compact and therefore space-saving unit. Additional transport units are no longer required. The mechanical connection is produced in the form of conveyor belts from KHS, which transport the bottles into the TLM systems, or the Transmodul from Schubert.
Based on the principle of scalability, the solutions are suitable for all sizes and can be expanded flexibly. With this solution, even smaller breweries have an opportunity to position themselves in the international trade with high-quality packaging.