Integration Key to Optimising Performance in Batch Processing
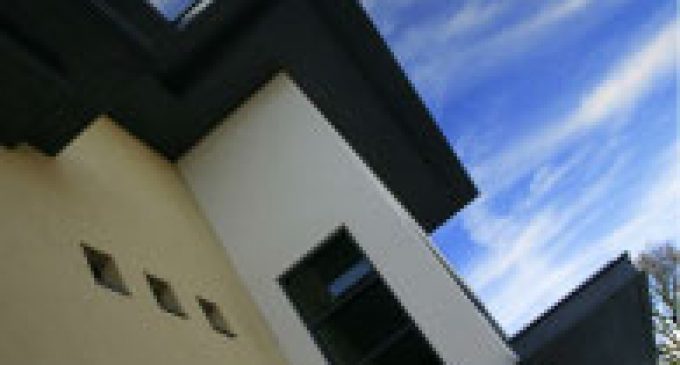
An integrated solution to optimise real-time performance, specifically designed for complex batch processes is now available through SolutionsPT, the automation and IT solutions provider for manufacturing and industrial clients.
Wonderware InBatch 2012 R2 is a new version of its already established InBatch software which incorporates System Platform to provide a unified answer to the complexities of batch processes, while still maintaining maximum flexibility.
Batches often have to endure handovers to other self-contained processes such as filling and packaging. The use of InBatch 2012 R2 removes the need to integrate these separate applications making production more time efficient.
By eliminating these islands of automation and replacing with this integrated set of manufacturing operations management, it is possible to lower costs and increase operational efficiency.
Sue Roche, Business Manager, Wonderware UK and Ireland, comments “Incorporating System Platform with existing InBatch technology to create this new software provides a unified application and information environment across the complete manufacturing process. By making batch management data available to users and systems throughout the plant, the software increases operational effectiveness and enables better levels of business optimisation in real time.”
SolutionsPT client, Akzo Nobel, has implemented InBatch at its plant in Birmingham – which produces packaging coatings primarily for the food and beverage industry – as part of an overhaul of its industrial IT technology.
InBatch has enabled AkzoNobel to deliver accurate, consistent recipes time after time, with the flexibility to add new recipes and production lines. Standardising the production process in this way ensures customer satisfaction with an end product which is of consistent quality and reduces the costs associated with the disposal of hazardous waste, which cannot be simply sent to landfill and is subject to stringent regulations and substantial disposal costs.
InBatch has also proved invaluable in being able to trace the exact provenance of every single batch which leaves the site, recording exactly what went into it and how it was created.