Improve Contaminant Detection and Food Safety with Dual Energy X-ray
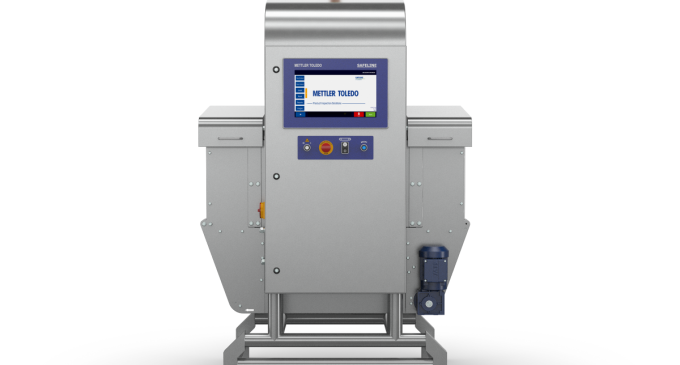
With certain products, food manufacturers can realise great benefits from using dual-energy x-ray
detection. Mike Pipe, Head of Global Sales of Mettler-Toledo Safeline X-ray, explains how the
technology can improve both inspection and business performance.
The detection of foreign body contaminants is part of the critical quality assurance process to
improve food safety standards. X-ray inspection has long been a key technology in this process, but
there are different types of x-ray detection with which food manufacturers can inspect their
products, depending upon the nature of the application.
Traditionally, manufacturers have used single-energy x-ray detectors, but dual-energy technology is
becoming more commonplace and is more powerful, effective, and easy to use than ever before. It
works using the concept of ‘material discrimination’, with dual x-ray beams of different energy able
to identify materials of different densities. Advances in detection sensitivity mean that dual-energy
x-ray is now even more discerning, allowing ever-smaller contaminants to be detected in a wider
range of applications.
But what are the applications in which dual-energy x-ray excels compared to the more commonplace
single-energy detection systems? In simple terms, there are two key aspects of a product that make
it suitable for inspection by dual-energy x-ray. The first is where there is a large degree of overlap
within the package, or where there are variations in thickness. Examples of the types of packs where
products overlap include packs of pasta, rice, nuts, and frozen goods such as French fries or potato
wedges. Packs with variations in product thickness include chicken breasts and other fresh cuts of
meat. Both scenarios produce an x-ray image with high levels of contrast.
The second type of application where dual energy x-ray is most suitable is where the likely
contaminant in a food product is a low-density material, such as glass, plastic, rubber, and calcified
bone.
If a product application has one or both of these aspects, then a case can be made for dual energy x-
ray. However, it is important to understand how this technology works. Here, the key concept is
material discrimination.
Dual-energy x-ray work by using high and low x-ray energy levels to discriminate between materials
of different densities. Software algorithms enable the material that is the food product to be
removed from a noisy x-ray image, leaving behind any material identified by the second energy level.
This is most likely to be a contaminant.
The most advanced dual energy technology available today features an enhanced detector that
collects detailed data about the product being inspected. When this is combined with sophisticated
image analysis software, the result is even clearer, higher resolution images that enable the best
levels of contaminant detection possible today.
Best fit
Mettler-Toledo dual energy x-ray systems can detect more than eight times as many difficult-to-find
contaminants as single energy x-ray systems. To ensure that a manufacturer’s application is best
suited to dual-energy x-ray manufacturers should look for a “Test Before You Invest” service.
The general rule of thumb is that dual energy is best suited to applications where some or all of
these factors exist:
- The product being inspected is one with high contrast, caused by overlapping products or
products with variable thicknesses. - The expected contaminants are low-density materials such as glass, rubber, plastic and
calcified bone. - The packaging material used is low density, allowing low-energy x-rays to pass through and
inspect the product inside.
Improving the effectiveness of contaminant detection with a dual-energy x-ray that is optimised to the
product application is clearly beneficial to food quality and consumer safety standards, but it also
helps the food manufacturer’s business.
Consider, for example, the degree to which the sensitivity of a single energy x-ray system would
have to be fine-tuned to detect very small contaminants such as 0.8mm pieces of stainless steel in
packs of nuts. The sensitivity required for such an application would very likely cause many false
rejects, which would result in a lot of product throwaways. Turning down the sensitivity to
reduce the false reject rate might mean that contaminated products pass undetected, leading to a
product recall and damage to reputation. Using dual-energy x-ray would very likely enable the
manufacturer to optimise detection around this application, without the resulting surge in false
rejects and wasted products. In turn, this makes the business case for dual-energy x-ray much
stronger.
Balancing wants and needs
Food manufacturers have to balance a range of factors, including budget constraints when deciding
upon investments and improvements to their production line capabilities, and product inspection is
only one of their considerations. It is a critical one though since it is the guardian of food safety.
With dual-energy x-ray, everything depends upon the application, including the nature of the
product, the possible contaminant, and the packaging. If operating on a tight budget, a single-energy
x-ray system might seem superficially more attractive. However, the more advanced contaminant
detection capabilities of dual-energy make a more accurate inspection of challenging applications
possible, and can quickly provide a return on investment, when set against the mounting costs of
waste through false rejects and potential product recalls.
For more information, please click www.mt.com/xray-de-wp-pr