Ilapak Fine Tune Bagging Equipment to Run New Compostable Film
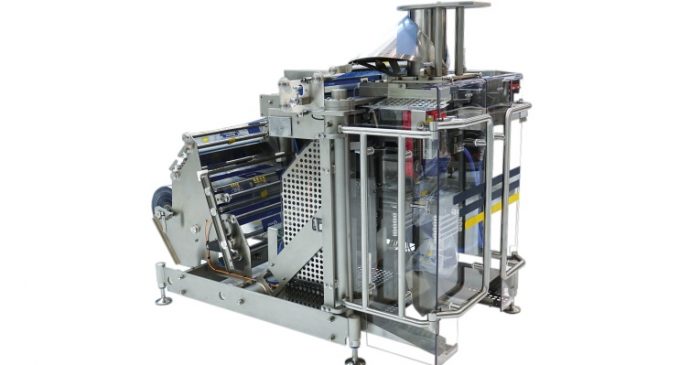
Responding to the rapid need for food factories to use sustainable packaging materials, Ilapak UK has successfully adapted one of its vertical flow wrapping systems, the Vegatronic, to run a new compostable film. Following this breakthrough, Ilapak plan to modify its entire fleet of over 1200 vertical and horizontal systems and offer an upgrade option to existing customers wanting to switch to environmentally friendly substrates.
From government through to consumers, the nation has waged a war to stamp out the use of non-recyclable plastics packaging*. Although sustainable polymer-based films are readily available, it is widely acknowledged that flow wrapping machines struggle to achieve a consistent pack seal due to the challenging characteristics inherent with compostable materials. Working together with innovative UK materials manufacturer Four04, Ilapak’s R&D department has developed a breakthrough heating techniques and a new sealing jaw coating to successfully seal EVAP – a clear, high-gloss film which offers a high moisture vapour transmission rate (MVTR) and is compostable to the EN 13432 standard.
Tony McDonald, Sales and Marketing Director at Ilapak, explains: “When you’re running standard oriented polypropylene (OPP) films, it doesn’t matter if the sealing jaw temperature varies by 10deg C or so. But to consistently seal a sensitive film such as EVAP, the jaws have to be non-stick. The heat has to be balanced across the element and you need accurate temperature control.”
The breakthrough came about when the EVAP film was being used to wrap organic own-label nuts for a major UK retailer. The breathable film holds special properties to lengthen shelf-life and, in particular, ensure that the nuts do not dehydrate.
Uniquely in the UK, Four04 also provides offline micro-perforation of its films, including the EVAP used in the nut bagging application. Crucially, the size and frequency of these perforations can be tailored in accordance with the specific respiration rate of the produce being wrapped, thus optimising shelf-life.
Nuts can lose up to 20% of their weight if they are allowed to dehydrate. This can have implications not only in cost but also in regulatory terms, given that suppliers have statutory obligations with regard to minimum weight.
FourO4 confirms that where EVAP has been applied to fresh produce packing in the past (including soft fruit, Brussels sprouts and new potatoes), the materials company has always partnered with machinery suppliers offering the most accurate temperature control for sealing. Technical Director at UK film producer Four04 Joe Ibbotson states: “Our film runs at typical commercial speeds and at lower temperatures.”
Sales and Marketing Director at Ilapak, Tony McDonald says: “Having successfully modified our Vegatronic VFFS machines, we’re pretty confident we’ll be able to upgrade our horizontal machines to run EVAP and other environmentally films too.”
Ilapak UK is committed to helping food factories reduce harmful plastics packaging.