How to stay on top of retailer COP curveballs
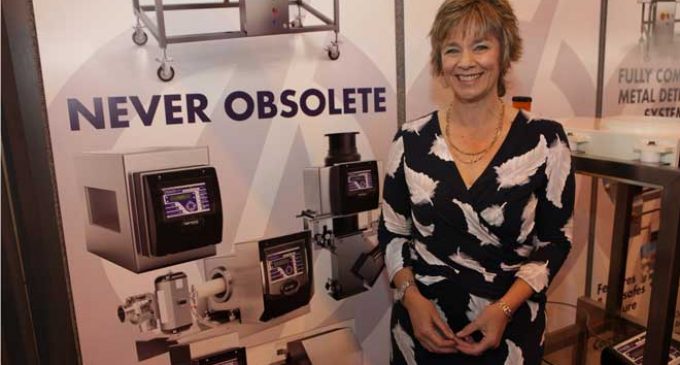
As well as legislative standards, when investing in metal detection equipment, food producers and contract packers need to stay mindful of the latest retailer Code of Practice (COP). Revised arrangements can swiftly leave a manufacturer vulnerable, with those failing to act potentially putting valuable contracts in jeopardy.
Demonstrating the regularity of these revisions, M&S refreshed its Foreign Body Prevention – Metal COP this August and updated them again in October 2015. Sarah Ketchin, Managing Director of Fortress Technology, speaks out about how the company’s backward compatible proposition helps manufacturers stay one step ahead of these COP changes.
“A major challenge for the food sector is each of the key grocery retailers will insist that manufacturers comply with their own COP,” comments Sarah. “When one introduces a new clause, the remainder major supermarkets tend to follow suit. Manufacturers then turn to their metal inspection suppliers for advice and immediate fixes.”
Tightening up on risks was the key driver behind M&S’s August COP revision, which specifically affected metal contaminant detection. Relating to Section 1.4.1, the revised clause sought to redress the issue of a system reboot clearing a fault. The precise wording states that: “If a detection system goes into a ‘fault state’, i.e. activation of a fail-safe or detector head fault, the system must be designed to maintain the fault state, even if the equipment is turned off and back on again.”
“When it comes to technology, especially computers, we can all be guilty of pressing the ctrl, alt delete buttons, or if a system freezes turning it off and back on again,” notes Sarah. “Realistically, this is unlikely to happen in a large production facility due to stringent operational protocols and what’s more, switching a machine off would impact on other lines creating a production bottleneck. Even in smaller plants, turning a machine off generally falls within the maintenance remit.”
No cutting corners in quality control
What this August COP revision raised was the potential hazard of contaminated product entering the supply chain. In metal detectors, a large majority of fault warnings are fixed – for example notification of a blocked photocell, low air pressure or full reject bin would still appear as a fault, even after a reboot. However, an event-based fault, for example a reject failure whereby the product was not seen entering the bin, could be wiped clean when powering the system up again. “This type of risk could result in a costly batch recall or re-inspection before shipping,” observes Sarah. “Retaining details of the last fault also requires the inspection device to have memory backup, which may not be a feature available in some older devices.”
Fortress swiftly resolved the situation for all of its M&S suppliers. This month the company issued a well-tested software update whereby any fault condition is re-displayed, even if an operative innocently turns off the power while the machine is active in order to clear the fault. “To minimise business interruption for customers we integrated the upgrade with a software update we’d already scheduled,” comments Sarah. The COP upgrade can be performed as part of a validation or routine maintenance visit, enabling M&S suppliers with Fortress Stealth and Phantom metal detectors to conform to the retailer’s audit requirements. The new release takes just several minutes to complete, minimising machine downtime.
Even perfectly functional yet older Fortress models won’t be obsolete as they too can upgrade to the latest electronics and USB data capture to meet evolving retailer standards.
Customers never treated as cash cows
Fortress is adamant that they are not in business to milk customers for money. In fact, it’s long been the company’s strategy to extend the lifespan of equipment and their Never Obsolete proposition is highly valued by customers. “When there’s a COP revision, the less scrupulous may try to sell you a new machine, which will naturally be a significant investment. That’s never been the Fortress way and many of our customers are realising the benefit of having kit that can easily and quickly be upgraded to meet the very latest standards.”
It was a real swing factor for Nutrition Group which ordered six Stealth metal detectors last year.
Tim Edwards, Facilities Manager at Nutrition Group said: “The problem with a lot of equipment is that it can quickly become outdated, but Fortress says that it will guarantee to support its metal detectors, even if I call them up needing a part in 10 years’ time. That’s a big commitment.”
Comparing the costs of purchasing a new machine versus a Fortress upgrade, Sarah remarks that for most businesses, it’s a bit of a no brainer. “An upgrade will only set a manufacturer back several hundred rather than thousands of pounds and the cost can be offset through the maintenance budget instead of eating into capital expenditure. What’s more, manufacturers can achieve instant compliance without having to wait for a new machine to be built and installed.”
Another notable benefit of a Fortress upgrade is no additional operative training is required – the menu and functional set up look and feel exactly the same. Nevertheless, Sarah is quick to point out that human error and misuse can never be totally eliminated by machines, however up-to-date they are. “It’s critical that company procedures and practices are robust and that operatives clearly understand their role and responsibilities.” Fortress offers training to build awareness of food safety risks and improve understanding among operatives.
“Changes to COP’s will understandably focus on fail safes and machine misuse, yet the improved sensitivity of today’s metal detectors shouldn’t be overlooked,” adds Sarah. “Many new metal detectors in the market today do challenge the traditional sensitivity expectations, especially for ‘wet’ products, and this is ultimately what minimises the risk of metal contaminated products entering the supply chain in the first place.”