GEA Builds New Dairy Powder Plant
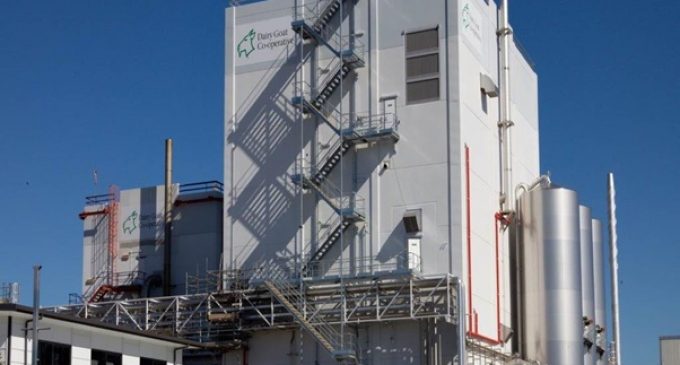
GEA Process Engineering in New Zealand has built a complete process plant for infant formula and goat milk powder for its long-term customer Dairy Goat Co-operative (DGC) in Hamilton. Working closely with DGC, GEA has used its experience in plant design to develop a highly innovative plant that provides multiple benefits including: improved product quality, reduced energy costs and reduced water consumption.
GEA has been a long-term partner with the Dairy Goat Co-operative since 2003 when it built the company’s original infant formula drying plant in Hamilton. The fundamental understanding of the company and its processes has helped GEA take a highly innovative, tailored approach to the design of Dryer 2. Despite the challenges of a tailored design, the project was completed in under 12 months.
Process Overview
The DGC plant produces 2.3 tonnes of highly formulated infant formula, and 2.7 tonnes of formulated base powders and goat milk powder per hour.
The process includes milk reception from farms in New Zealand’s central North Island followed by heat treatment, separation and dosing of vegetable oils, powders, vitamins and minerals; concentration using falling film evaporators; spray drying; and packing into bulk bins and, once quality is assessed, packing into retail cans. The system also filters exhaust air to remove particles before releasing it into the environment. Throughout the process the system is designed to minimize power and water usage in line with the company’s sustainability objectives.
Innovating For Quality, Profit and the Environment
Dryer 2 at the Hamilton site includes a number of innovations tailored to DGC’s requirements:
Falling Film Evaporators
The multiple effect falling film evaporators are designed to handle batches of formula with elevated total solids which provides DGC with a saving in its annual energy costs it also means less energy is required from non-renewable energy sources with a resulting positive impact on the environment.
Computer Optimised Plant Design
GEA has modelled the drying processes within the dryer using Computational Fluid Dynamics running on its most powerful computers. This allowed the dryer shape and size to be optimised to require less frequent cleaning while still minimising the size and visual impact of the dryer tower building. Air supply to the dryer ensures even temperature and air flow distribution to improve dryer performance and minimise energy consumption.
Continuous Dryer Operation
Twin evaporators, each capable of a day’s operation prior to cleaning, cycle in turn to maintain a continuous feed to the dryer. In this way the dryer can be run continuously for many days before it too must eventually be stopped and cleaned. This is only the second infant formula dryer in the world to be set up for continuous dryer operation in this way. This technique improves dryer utilisation, increases powder output and reduces energy consumption. Less cleaning also reduces the consumption of resources such as energy and water.
Dryer Dehumidification
The customised desiccant dehumidifier continuously reduces and controls the humidity of the incoming air used for drying. This is the first time this type of technology has been used on a spray dryer in NZ. The dehumidifier allows the dryer to run closer to its optimum efficiency while maintaining capacity even during periods of higher ambient humidity and humidity fluctuations that would normally have a substantial impact on the performance of the dryer. One of the side benefits of dryer air dehumidification is that during the moisture adsorption process the air is heated by as much as 25°C for free.
Dryer Exhaust Air Recuperation
To improve energy efficiency and reduce waste heat losses a specially designed recuperation heat exchanger has been fitted by GEA to the exhaust stack to recover the energy from the exhaust air. This is the first such system installed on a dryer in NZ. The energy from the exhaust air is used to generate hot water. The hot water is then used during cold days to preheat the air used for drying, and on hot and humid days is used for regeneration of the desiccant dehumidifier system.
“We have had a very good relationship with DGC for a long time,” said Barry Cole, Business Development Engineer for GEA Process Engineering in New Zealand. “By working closely together we have been able to include innovations at the Hamilton site, many of which have not been seen before in New Zealand. We are all delighted with the outcome.”
“GEA has worked very collaboratively with DGC to design a flexible plant that meets the high standards required of an infant formula facility”. Brent Prankerd, General Manager Manufacturing for DGC also commented “We are pleased with the functionality and quality of the plant installed and the quality of the product being produced on the new drying facility.”