EU project aims to produce plastics from biomass
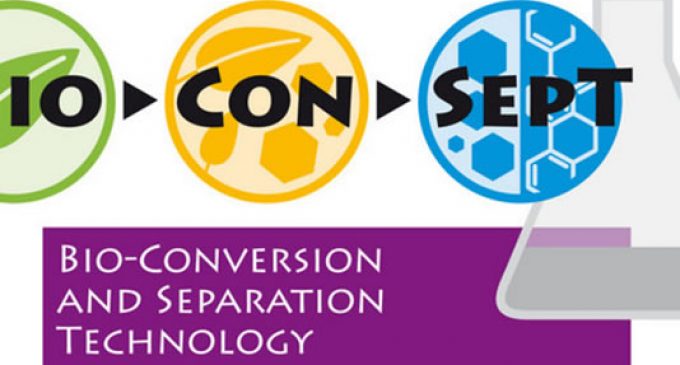
Food and beverage plastic packaging is one possible end application for an EU project which aims to create platform chemicals from second generation biomass.
BioConSepT targets using white biotech processes that convert second generation biomass into valuable bi-functional platform chemicals (short and medium chain length di-acids) for bioplastics.
The project aims for commercial applications that would be 30% cheaper and 30% more sustainable than the conventional chemical route or first generation process like glucose and starch which are used in food.
The focus is on the use of so-called second generation feedstocks like lignocellulose and non-edible oils and fats, which cannot be used for the production of food.
Building blocks
In the lignocellulose chain raw materials such as C5-C6 sugars will be converted and separation into FDCA, itaconic acid and succinic acid before the demonstration process.
In the oils and fats chain, fatty acids and glycerol will be converted and separated into long chain di-carboxylic acids, amines and epoxides for the second demonstration.
The project will deliver samples of the envisioned applications, which include green polymers, resins, plasticizers, surfactants and solvents for testing in the market.
Dirk Verdoes, TNO chief technology officer in the department process and instrument development, told FoodProductionDaily.com that they had made progress in feedstock supply and converting the feedstock into platform chemical.
“The next step is about integrating the results and connecting between the different steps in the process…some parts are moving very well and with others we know where we need to focus on.”
He said that people are recognising the potential of biomass and the need to be successful in converting from conventional methods.
“In society at the moment you see like one day or another there will be not enough oil and gas to do what we currently do. Society and industry needs to make a change where it is possible.
“In the current situation there are no industry processes, that I know of, to convert second generation feedstock into valuable chemicals.
“The reasons include the knowledge is not yet at the stage and the expertise is not at the stage to move to a profit in the design and building of a factory.”
One of the raw materials they are working with at the moment, FDCA, is a green alternative for use in polyethylene terephthalate (PET) bottles, which would then become polyethylene furanoate (PEF) added Verdoes who compared it to Avantium’s method but using different processes .
Project set-up
In the third year BioConSepT will select the two most promising two chains out of the seven being examined for demonstration at a scale of 100 to 1000kg product by the fourth year.
In a recent project update, Jan Harm Urbanus, project lignocellulose chain manager and technology manager Biobased Economy at TNO, wrote that while there had been significant process in the development of biotechnological production systems, challenges remained.
“Breakthroughs are still required in the production of cheap feedstocks, and in particular cheap HMF (5-(Hydroxymethyl)furfural) which is a toxic but highly valuable by-product of biomass treatment.”
The project aims to reduce the gap between the laboratory and industrial practice for the production of chemicals from abundantly available biomass.
Davide Perini, lab manager and principal investigator for biotechnology laboratory at Novamont, said the firm was mostly interested in using modified fatty acid as monomers in polymer synthesis for (bio)plastic production in the same update.
“We will characterise the innovative (bio)polymer from a chemical and physical point of view. Finally we test them in different formulations aiming to produce biodegradable and compostable bioplastic.”
The consortium is coordinated by TNO (Netherlands Organization for Applied Scientific Research) and consists of 31 partners from research and technology organizations, large industrial companies and small and medium-sized enterprises.
Partners include VTT (Finland), Fraunhofer (Germany), ADM Europe (Netherlands), Evonik Industries (Germany), Novamont (Italy), Biochemize (Spain) and Ingenza Company (UK).