Bürkert success story – New control heads at Fromagerie Bel in the Meuse
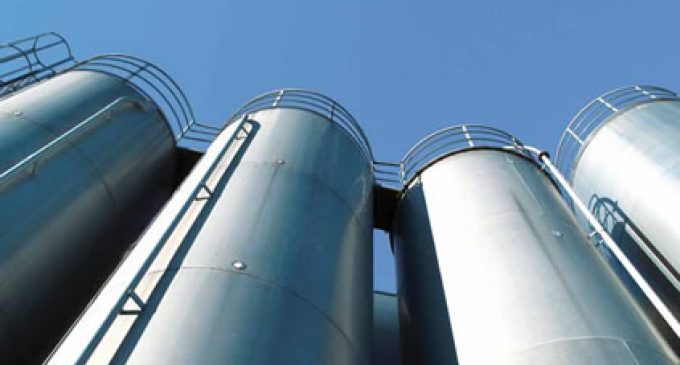
At its Cléry-le-Petit site in the Meuse, Fromagerie Bel wanted to add an extra protein constituent to the milk collected locally in order to guarantee consistent quality of the cheese produced. TETRA PAK constructed a new system in which flow management is handled by 180 fieldbus controlled valves. Bürkert supplied 180 control heads to be fitted to the valves. Providing optimal reliability and safety, the new series 8681 control head is particularly suited to aseptic environments as it offers hygienic design, IP65/67 protection rating and good resistance to chemical cleaning products. In addition, Bürkert’s patented magnetic activation system provides easy and safe access to the control head for preventive maintenance.
A leading group in agrifood production
Fromagerie Bel markets its five star brands (La Vache qui Rit, Mini Babybel, Kiri, Leerdammer, Boursin), as well as more than 20 local brands with a strong image, on five continents. Among these local brands, for example, we can mention Apericube in France and Japan, Régal Picon in Africa and the Middle East, Shotska in Ukraine and Maredsous in Belgium.
The Group, which employs 11,300 people, achieves a turnover of 2.4 billion euros and has 25 production sites throughout the world. It recently approached TETRA PAK for an industrial project at its Cléry-le-Petit site in the Meuse, which processes 110 million litres of milk and produces 12,000 tonnes of cheese per annum. Indeed, TETRA PAK designs and installs numerous systems based on tried and tested technologies used to produce various kinds of cheese (Emmental, Raclette, St Paulin, Cheddar, Mozzarella, Gouda, Edam, Mimolette, cottage cheese, cream cheese and other soft, unripened cheeses). Its equipment (particularly cheese vats) is currently used in cheese production processes marketed throughout the world.
The project to enrich the milk’s protein value
Fromagerie Bel‘s project at its Cléry-le-Petit site was intended to add an extra protein constituent to the milk collected locally in order to guarantee consistent quality of the cheese. Indeed, the milk collected in the region is quite low in proteins, which makes it just about usable for cheese production. Moreover, although the milk, which represents 50% of the price of cheese, is not sufficiently rich in proteins, a more significant quantity of lactoserum with no added value still remains, at the expense of the cheese factory.
To solve this problem, new vats were therefore installed. Flow management is handled by fieldbus controlled valves. Bürkert, the manufacturer of measuring and flow control equipment, supplied the series 8681 control heads, offering control and diagnostic safety thanks to the remote visualisation of the position of the valve.
Among the other advantages provided by this new equipment, it is possible to eliminate water hammer in the pipework thanks to the opening and closing speed settings of the valve. Furthermore, IP 65/67 tightness in accordance with the EN60529 standard is guaranteed by the fact that the control head is no longer opened on site after commissioning (magnetic control key) and thanks to its pressurisation. These instruments also offer the possibility of ASI communication. This project has thus enabled the standardisation of the control heads on every valve used on the site. In total, 180 control heads were supplied.
The technical characteristics of the new control Heads
The new series 8681 control head was especially developed by Bürkert for the decentralised automation of santary globe, butterfly and ball process valves. It complements the control heads, digital positioners and process controllers in Bürkert‘s ELEMENT range and is used to equip automation facilities for the dairy, brewery and other food and beverage industries.
This new, universally adaptable control head can therefore be installed on all types of valves available off the shelf, like globe valves (single, double globe and Mixproof), butterfly valves and ball valves. It is particularly suited to aseptic environments thanks to its hygienic design, its protection rating and its resistance to chemical cleaning products. In the context of decentralised automation concepts with fieldbus communication protocols, the control head executes all pneumatic commands, position feedback functions and diagnostics. Depending on the process valve, it can control up to three pneumatic chambers separately.
This new control head is easy to install, use and check. The respective positions of the process valve are checked by the control head via an inductive analogue position sensor. After installing the control head on the valve actuator, the positions of the valve are determined automatically by a fast, reliable „teach-in“ function, which eliminates any need for configuration and manual adjustments. For some Mixproof valves, a fourth valve position can be checked by an inductive proximity switch mounted on the outside.
The opening/closing time of each pneumatic chamber is checked and adjusted individually for two circulation directions thanks to a flow limiter function integrated in the pilot solenoid valve. Moreover, a check valve prevents opening/closing of the valve in the event of back pressure. Independently of the electric power supply, each pilot solenoid valve can be switched manually with a manual mechanical control. The encoded and patented manual magnetic control is used during valve maintenance to switch the actuator without having to open the control head, which prevents any pollution inside the head (humidity, dust, spatter, etc.).
In addition to the electrical duplication of the valve positions in the controller, a large format visual luminous colour display unit signals valve positions, operating errors, anomalies in communication with the bus, mechanical blockages in the valve, etc.. Internal diagnostic data, like the number of cycles for servicing the valve seals or operating errors, are therefore signalled visually and archived in the memory; they can be read in detail via a service interface (SmartPhone or PC).
The decentralised automation of process valves
The decentralised automation of process valves offers a number of advantages. Compared with a solenoid valve block in a centralised control cabinet, control heads mounted directly on to the actuator simplify planning, installation, start-up and maintenance by significantly reducing the connections required. The switching time and the consumption of pilot air are minimised thanks to extremely short pipes between the pilot solenoid valve in the control head and the pneumatic actuator. The concept of decentralised automation therefore makes it possible to clearly structure and easily monitor the installations, which enhances operational reliability.
The series 8681 control head enables instant visual diagnostics of valve status by colour coding (Open/Closed/Error) that can be seen from quite a distance (100 metres). This innovative equipment permits universal use on all types of valve. Designed using hard-wearing synthetic materials, it enables preventive maintenance thanks to the archiving of usable data on PC. The useful life of the system is increased by an inductive non-contact sensor, as well as by the IP 67 protection rating, pressurisation and self-ventilation of the head.
Communication is easy thanks to Bluetooth via SmartPhone and/or PC (for valves difficult to access). The unit as a whole eradicates any risk of external contamination thanks to a hygienic and aesthetically pleasing design. Maintenance is safe and facilitated by external magnetic activation (system patented by Bürkert). In addition, start-up times are reduced by the simple self-setting limit switches (AUTOTUNE function). Switching is secure thanks to the pneumatic solenoid valves.
Company contacts
Bürkert Fluid Control Systems
Christian-Bürkert-Straße 13 -17
74653 Ingelfingen
Germany
Tel. +49 (0) 7940/10 – 0
Fax +49 (0) 7940/10 – 91 204
info@burkert.com
www.burkert.com