The OCME DryBlock® – A New Way to Design, Build and Manage End of Line Bottling
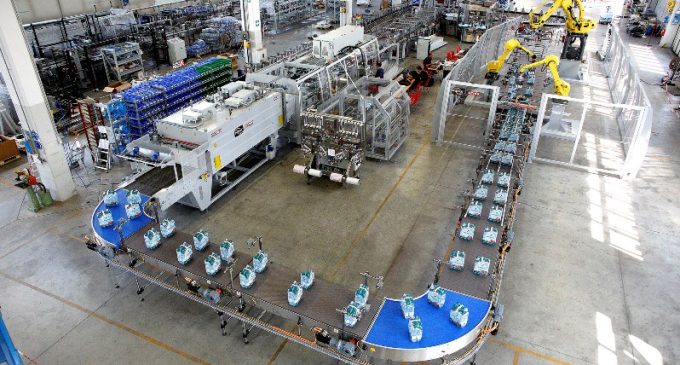
The new OCME DryBlock® was presented to visitors attending the Drinktec 2013 exhibition. The DryBlock® system is a new way to design, build and manage the whole end of a bottling line. It combines the entire dry part of the line into a single, integrated and synchronized ‘Monobloc’ – several machines working together as one.
DryBlock® is designed to meet the needs and growing demands that come from the consumer goods industries, including:
* Increase in efficiency: the overall efficiency of a line with DryBlock® system is greater than the sum of the efficiency of the individual units.
* Cost reduction: a single operator can manage the entire end of the line thanks to a number of innovative features inside the single machines and the whole system.
* Reduction of energy consumption by up to 36%: low energy features on machines and reduction in the number of conveyor drives.
* Space reduction: in a space of only 35×14 meters, a complete end of line, from the labeller to palletiser, thanks to DryBlock technology.
* Unprecedented levels of flexibility: format changes are automated and made quickly, for a wide range of bottles or containers, even hard to handle bottles with shaped forms and light materials.
A Modular Logic
DryBlock® is designed as a modular system that can be adapted to the needs of numerous industrial sectors. The various modules can include a labeller (or a sleever), a packaging machine (shrinkwrapper, trayformer, wrap-around, pick & place, combi, etc) and a palletising module that typically consists of a layer formation unit (manipulators) and one or more robots – or alternatively, traditional palletisers.
A Single Operator
The DryBlock® system is controlled by a single operator who is located in a central position with respect to the whole plant. Here the operator can monitor the status of each component and govern the operating parameters through a single interface.
Ergonomics and Safety: Ethics is Not an Option
DryBlock® expresses the attention of OCME for the quality of the work environment and respect for the highest standards of safety. Some important measures have been adopted in crucial points such as:
* Shorter distances for the operator.
* Simplified label change.
* Automatic label splicer.
* External and integrated reel holder, ergonomic and easy to reach.
* Integrated handle applicator, placed outside the machine.
* One operator panel.
* Automatic film splicer.
* Maximum safety standards with CE compliance.
* Reduced noise thanks to the reduction of components and accumulation.
An important part of the DryBlock® logic is the rationalisation of the product flow. This has led to the elimination of accumulation, with the benefit of reducing friction and contact between containers. This reduces the risk of damage to the product, even when running ultra-light, fragile, delicate or unstable containers.
Easy to implement
Solutions based on the DryBlock® system come as a “turn-key” process, in order to simplify and speed up the start-up at the customer premises, with obvious practical and economic advantages.
Scalability
One great advantage of the DryBlock® logic is the option to defer the investment by purchasing different components at different times. In this case, each module is designed to integrate and “dialogue” with the DryBlock® control center. This actually makes DryBlock® “scalable”; in fact, it can grow along with the needs of the company.
For further information contact OCME UK Ltd, sales@ocme.co.uk, Tel. +44 (0)1635-298171.